Posted on May 01, 2024
Low pressure moulding offers distinct advantages over traditional potting, starting with enhanced protection for sensitive electronics. Utilising specialised polyamide materials, this process provides exceptional resistance to moisture, chemicals, and extreme temperatures. This ensures the longevity and reliability of encapsulated components, making it particularly suitable for demanding applications.
Efficiency is another significant benefit of low pressure moulding. The process is notably faster than traditional potting, with shorter cycle times and no need for extended curing phases. This increased efficiency translates to higher throughput and reduced production costs, a clear advantage for manufacturers aiming to optimise their operations.
Precision in encapsulation is a hallmark of low pressure moulding. The materials flow smoothly around components, filling voids without exerting excessive pressure that could damage delicate parts. This level of precision reduces the risk of encapsulation-related defects and enhances the overall quality of the final product.
From an environmental perspective, low pressure moulding is a more sustainable option. The materials used are generally more eco-friendly, and the process generates less waste compared to traditional potting techniques. This not only helps manufacturers meet sustainability goals but also aligns with the increasing demand for greener production practices.
Design flexibility is another area where low pressure moulding excels. It allows for the creation of complex shapes and custom solutions tailored to specific applications. This flexibility is invaluable in industries such as automotive, aerospace, and consumer electronics, where unique encapsulation challenges are often encountered.
In contrast, traditional potting, while effective, tends to be more time-consuming and can place greater stress on electronic components. The curing phase required in potting can slow down production and increase costs. Additionally, potting materials may not provide the same level of environmental protection as the specialised materials used in low pressure moulding.
In conclusion, from our perspective as a forward-thinking manufacturer, low pressure moulding often proves to be a better choice than traditional potting. Its advantages in terms of protection, efficiency, precision, sustainability, and design flexibility make it a superior encapsulation method for modern electronic components. By adopting low pressure moulding, manufacturers can enhance product performance, reduce costs, and achieve a competitive edge in the market.
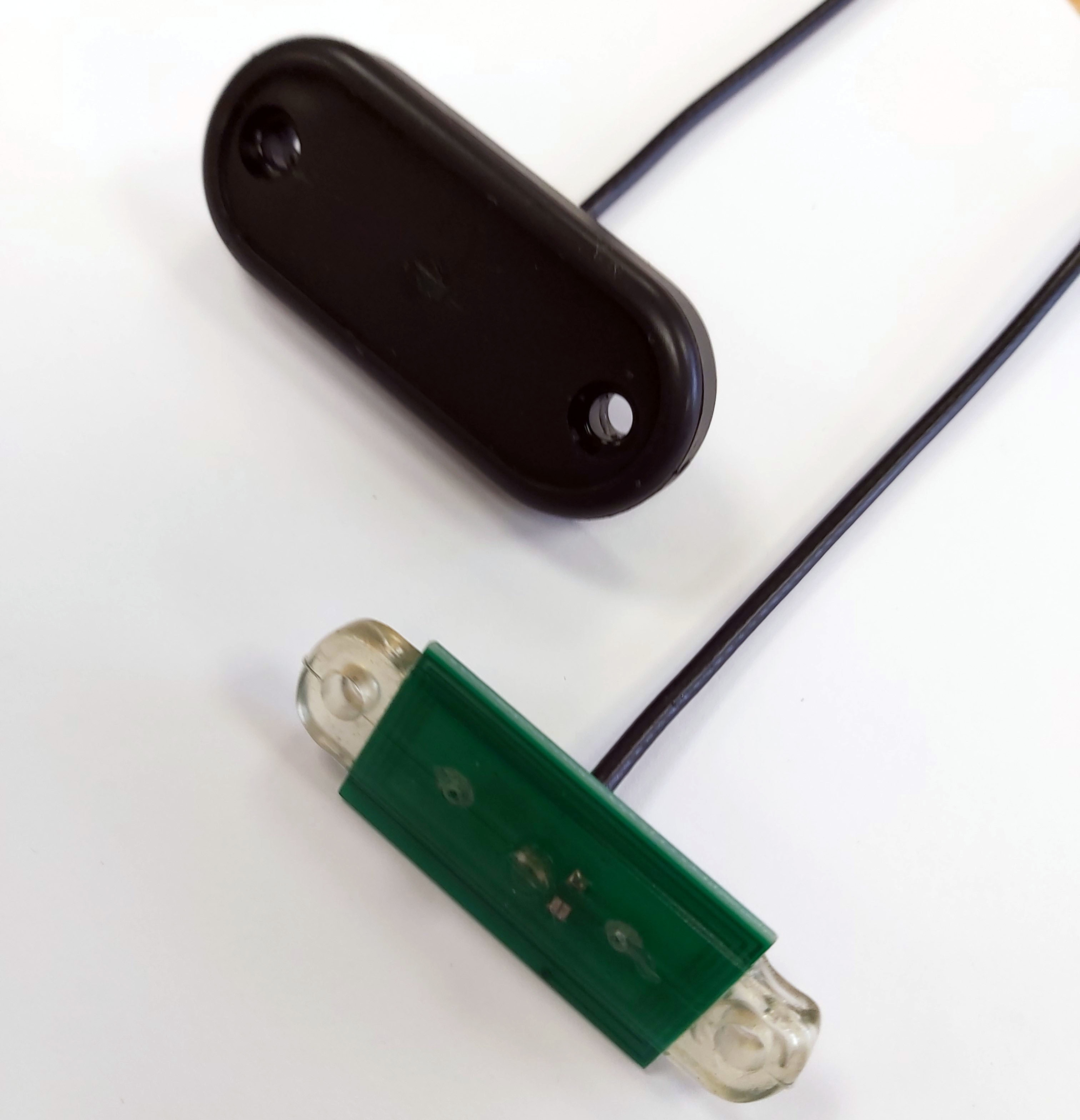