Posted on June 13, 2024
What is Cable Harness Manufacturing?
Cable harness manufacturing involves the design, assembly, and production of bundles of wires and cables, which are used to transmit electrical signals and power across various systems. These harnesses are meticulously crafted to meet specific electrical and geometric requirements, ensuring optimal performance and reliability in diverse applications.
Why Cable Harnesses Are Essential
- Organized Wiring: Cable harnesses neatly bundle together numerous wires, reducing the risk of tangling and making systems more manageable.
- Enhanced Safety: By securely binding cables, harnesses minimize wear and tear, thereby reducing the potential for electrical shorts or failures.
- Improved Performance: Custom cable harnesses are designed to meet precise electrical and mechanical specifications, ensuring optimal functionality and efficiency.
- Space and Weight Efficiency: Harnessing cables together can save significant space and weight, crucial in industries like aerospace and automotive.
The Cable Harness Manufacturing Process
The process of cable harness manufacturing is a blend of meticulous planning, precise engineering, and skilled craftsmanship. Here’s a step-by-step overview of how a typical cable harness is created:
1. Design and Planning
The first step in cable harness manufacturing is designing a blueprint that meets the specific requirements of the application. This involves:
- Detailed Specifications: Determining the type and length of wires, connectors, and any protective materials needed.
- Schematic Diagrams: Creating detailed diagrams that outline the wiring configuration and routing paths.
- Component Selection: Choosing appropriate wires, connectors, and protective materials that comply with industry standards and client needs.
2. Prototyping
Before full-scale production, a prototype of the cable harness is built to ensure it meets all design and functional requirements. This phase includes:
- Assembly of Components: Manually assembling the wires, connectors, and protective materials as per the design.
- Testing and Validation: Rigorously testing the prototype for electrical continuity, insulation resistance, and mechanical durability.
3. Assembly
Once the prototype is validated, the assembly process begins, often involving the following steps:
- Cutting and Stripping: Wires are cut to specified lengths and stripped to expose the conductors.
- Crimping and Soldering: Connectors are attached to the wires through crimping or soldering, ensuring a secure electrical connection.
- Bundling and Securing: Wires are bundled together using ties, sleeves, or tapes to form the harness.
- Overmolding: In some cases, an additional protective layer is applied over the harness to provide extra durability and environmental protection.
4. Testing and Quality Control
Quality is paramount in cable harness manufacturing. Comprehensive testing is conducted to ensure the harness meets all performance standards:
- Electrical Testing: Verifying electrical continuity, insulation resistance, and signal integrity.
- Mechanical Testing: Assessing the harness’s ability to withstand mechanical stresses, such as vibration and flexing.
- Environmental Testing: Ensuring the harness can perform under various environmental conditions, such as temperature extremes and humidity.
5. Packaging and Delivery
The final step is packaging the completed cable harnesses and preparing them for delivery. Proper packaging is essential to prevent damage during transportation and storage.
Factors Influencing Cable Harness Quality
Quality and precision are crucial in cable harness manufacturing. Several factors influence the final product’s quality:
- Material Selection: Using high-quality wires, connectors, and protective materials is essential for durability and performance.
- Manufacturing Techniques: Advanced assembly techniques, such as automated cutting and crimping, enhance consistency and accuracy.
- Testing Protocols: Rigorous testing ensures that the harnesses meet all electrical, mechanical, and environmental specifications.
- Skilled Workforce: Experienced technicians play a vital role in assembling and inspecting cable harnesses to ensure top-notch quality.
Advances in Cable Harness Manufacturing
The industry is continually evolving, driven by technological advancements and increasing demand for more complex and reliable connectivity solutions. Some notable trends include:
- Automation: The use of robotic systems and automated processes to improve efficiency and precision in assembly.
- Advanced Materials: The development of new materials that offer better performance, such as high-temperature or high-flexibility wires.
- Miniaturization: As devices become smaller, the need for compact and lightweight cable harnesses is growing.
Conclusion
Cable harness manufacturing is a critical component in the modern technological landscape. From simplifying complex wiring systems to enhancing the safety and performance of various applications, cable harnesses are indispensable. As the demand for sophisticated connectivity solutions continues to rise, the importance of high-quality cable harness manufacturing cannot be overstated.
If you are in need of expert cable harness manufacturing services or looking to learn more about how these vital components can benefit your operations, feel free to contact us. Our team of experienced professionals is ready to assist you in creating custom solutions that meet your specific needs.
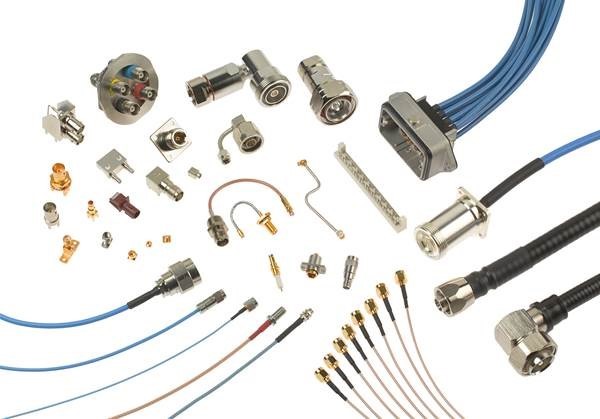