Posted on October 26, 2018
Wire looms are a big part of what Greenstock in-connect offer. And, while we, and our clients, interchange the terms we use to describe a loom / cable assembly / wiring harness…for some the terminology alone can be a tad confusing. So, in celebration of the wiring loom (and, to make things a little simpler) we’ve compiled a bit of a fact sheet about wiring looms. We hope you find it interesting.
What is a wiring loom?
A wire loom or wiring harness or cable assembly is a collection of wires and cables that distribute electrical signals in the most efficient way possible. The cables and wires are linked together using straps, cable ties, sleeves, electrical tape, conduit, and weave.
History of wiring looms
Wire Looms were created to offer a solution to the ever-increasing amounts of cables that manufacturers were using to connect electrical components in their products.
The automobile sectors were early adopters of wire looms. Vehicles builds pre 1920s were originally designed using individual cables that were exposed within the engine bays, these cables were subject to wear and tear making it a costly expense to the customer to replace.
Engineers found that binding the many wires and cables into a wire loom allowed the wires and cables to be better secured against the adverse effects of vibrations, abrasions, and moisture.
The Aerospace industries were also using masses of single wires in their aircraft builds that would stretch over several kilometers if fully extended. By combining the wires into large scale looms it allowed for a more cost effective build and a safer aeroplane.
The 1920s also saw a boom in electrical household goods; steam powered products were being replaced in many homes by electrical white goods – washing machines, Irons, fridges, vacuum cleaners all designed using many small components and connected by complex individual wiring systems. Manufacturing these products for mass production was often a timely and a costly process and by introducing pre-assembled wiring looms, manufacturers offered a timelier more cost effective build.
As technology advanced the need for more bespoke wiring solutions were required for technology such as telephones, televisions, film projectors and gramophones in the 1930s.
Wiring loom designs needed to be greatly reduced in size and weight to accommodate these compact builds.
By the 1940s, military technology had advanced and electronic components were now standard fittings in designs of tanks, fighter planes, warships and field communication devices. Military assembly lines were hastily assembled with the demand on speed of production.
The 1950s saw growth in the manufacturing of electric heat, air conditioning, water heating, and cooling systems. Heating and cooling elements were housed together with accompanying components in full box build assemblies. The potential for electrical corrosion was great in these types of builds so wiring looms had to be designed to precision using protective shielding and terminals to eliminate any possible hazard.
Modern wiring looms come in all shapes and sizes, they can incorporate a massive range of connection types, include electronic PCB’s, relays and other electronic components. Overmoulding of connectors and components is also common place enabling very robust products, custom glands or strain reliefs and encapsulation of components such as ferrite cores or PCBs.
History of
We commenced trading in 1993 at a site in Lincoln. In the early days the company formed close working relationships with a number of leading OEM's in the health and leisure sector. Through these relationships the company developed a variety of customer specific connectors and cable assemblies for battery operated equipment. In some cases the products designed have become industry standards within these specific markets.
The ability to provide design solutions to customer cable and connectivity problems saw the company rapidly grow and to become a prime source of supply to a number of high profile brand leaders.
These innovative designs led to the business enhancing its overmolding capability and this created further opportunities as customers recognised the benefits of an integral connector configuration as opposed to discrete components. This experience lead onto the overmoulding and encapsulation of PCBA's, discrete components and other insert types and has become a key competency of the company.
The company continues to invest in capital equipment particulate to support its moulding capabilities and recently in an additive manufacturing capability to support its design and development activities.
The company has continued to extend its client base worldwide, and now exports to 15 countries, with customers in the USA, Canada, Europe and Asia.
If you would like to find out more about Greenstock in-connect or would like a quote for your then please contact our friendly sales team they will be happy to help.
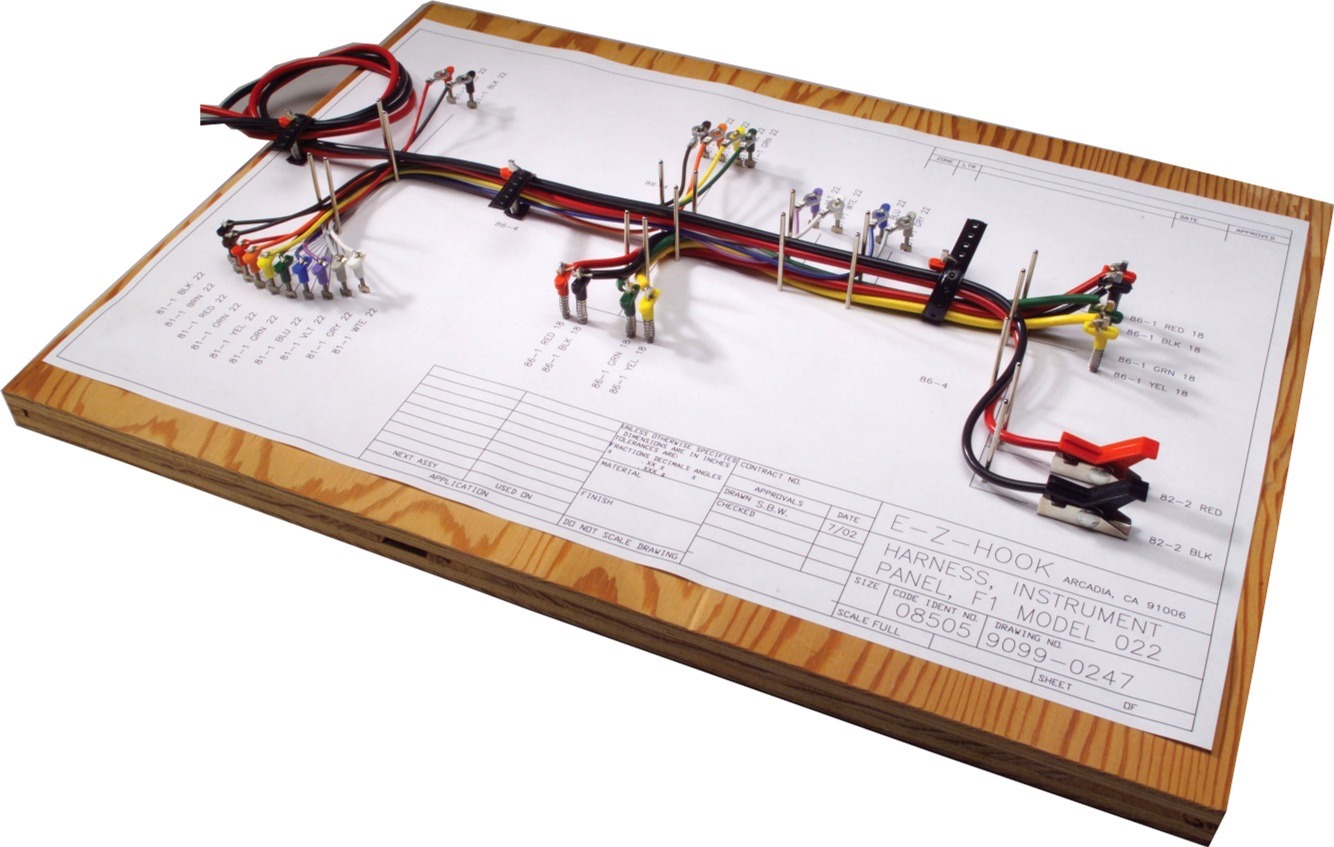