Posted on July 16, 2024
Low pressure moulding (LPM) is emerging as a compelling alternative to traditional potting techniques for encapsulating electronics. As a manufacturer deeply invested in the advancement of electronic component protection, we recognise the distinct advantages that LPM offers, which can significantly enhance the manufacturing process and the quality of the final product.
One of the primary benefits of low pressure moulding is its ability to provide superior protection for sensitive electronic components. The process involves using specialised polyamide materials that offer excellent resistance to moisture, chemicals, and extreme temperatures. This ensures that electronics are well-protected against environmental factors that could compromise their functionality and longevity.
Moreover, low pressure moulding is a more efficient process compared to traditional potting. The moulding cycle is typically faster, reducing production time and increasing throughput. This efficiency is further enhanced by the elimination of the need for a curing phase, which is a requirement in many traditional potting techniques. The result is a more streamlined production process that can lead to significant cost savings.
Another notable advantage of LPM is the precision it affords in the encapsulation process. The moulding materials flow smoothly around components, filling gaps and voids with minimal stress on the parts. This precise application reduces the risk of damage to delicate electronics, which is a concern with higher pressure potting methods. Additionally, the materials used in LPM adhere well to a variety of substrates, ensuring a strong bond and effective encapsulation.
From an environmental standpoint, low pressure moulding is also a more sustainable option. The materials used are often more eco-friendly, and the process itself generates less waste compared to traditional potting methods. This aligns with the growing demand for greener manufacturing practices and can help companies meet their sustainability goals.
In terms of design flexibility, low pressure moulding offers considerable advantages. It allows for the creation of complex shapes and custom solutions tailored to specific applications. This flexibility can be particularly beneficial in industries such as automotive, aerospace, and consumer electronics, where unique encapsulation challenges are common.
In conclusion, as a manufacturer committed to delivering high-quality, reliable electronic components, we find low pressure moulding to be a superior alternative to traditional potting techniques. Its benefits in terms of protection, efficiency, precision, environmental impact, and design flexibility make it an excellent choice for modern electronic encapsulation needs. Adopting LPM can lead to enhanced product performance and significant competitive advantages in the marketplace.
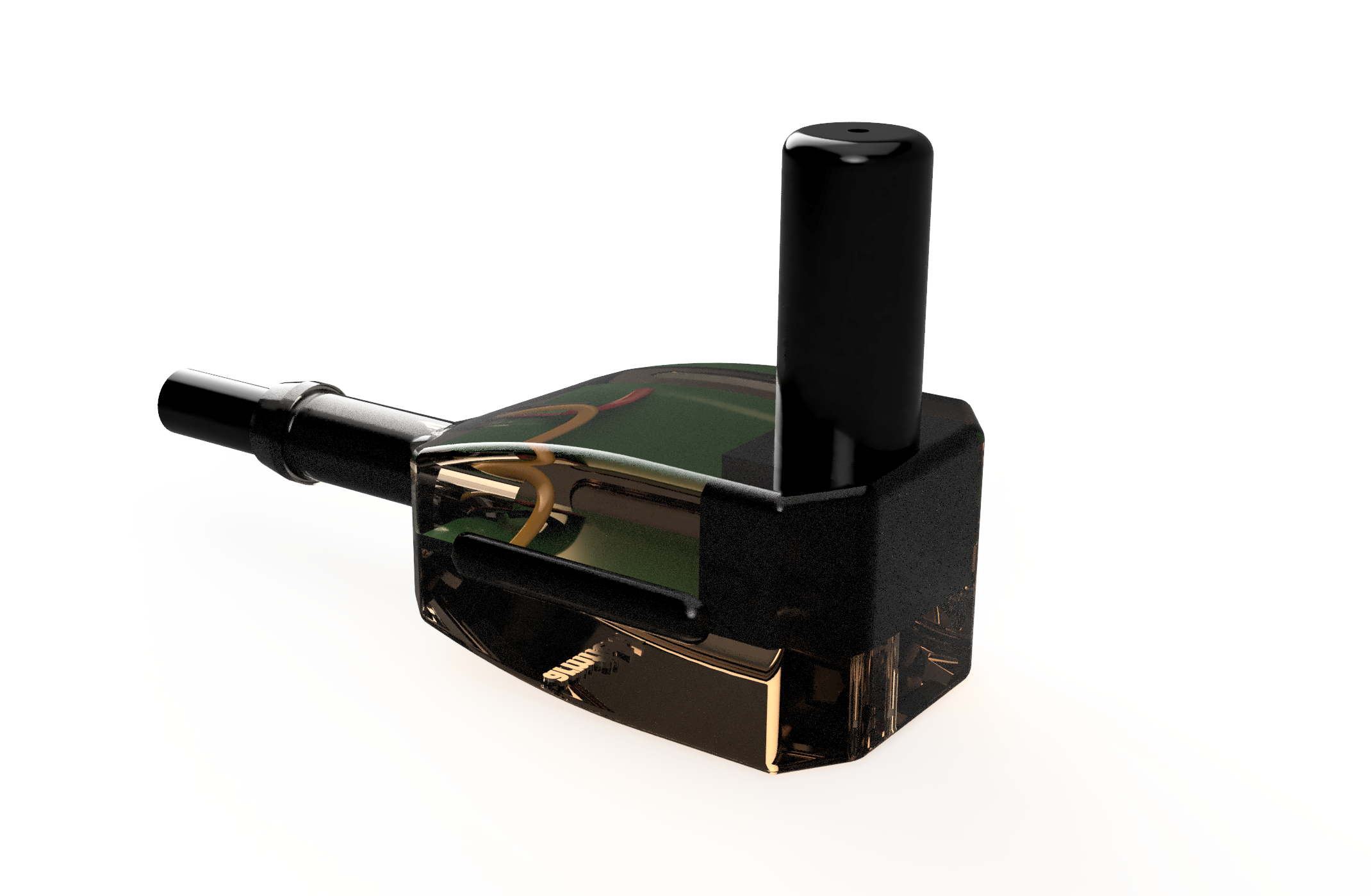